The shareholder and the engineer
In the mid 60’s, Alexander Tutsek, the later shareholder of Refratechnik, was searching for a raw material: Silicon oxide (SiO2). He needed it for the growing product portfolio of today’s largest family-owned company for refractory products. His search also took him to the beautiful region of Piedmont in Italy.
There, in the small town of Trino, lived the Bertolotti family. The father was acquainted with Alexander Tutsek. The son, Danilo Bertolotti, is now Managing Director of Refratechnik Italia. Danilo, an inquisitive, technically gifted young man, will be largely responsible for one of the most sustainable innovations in Refratechnik’s history. And that has a lot to do with rice.
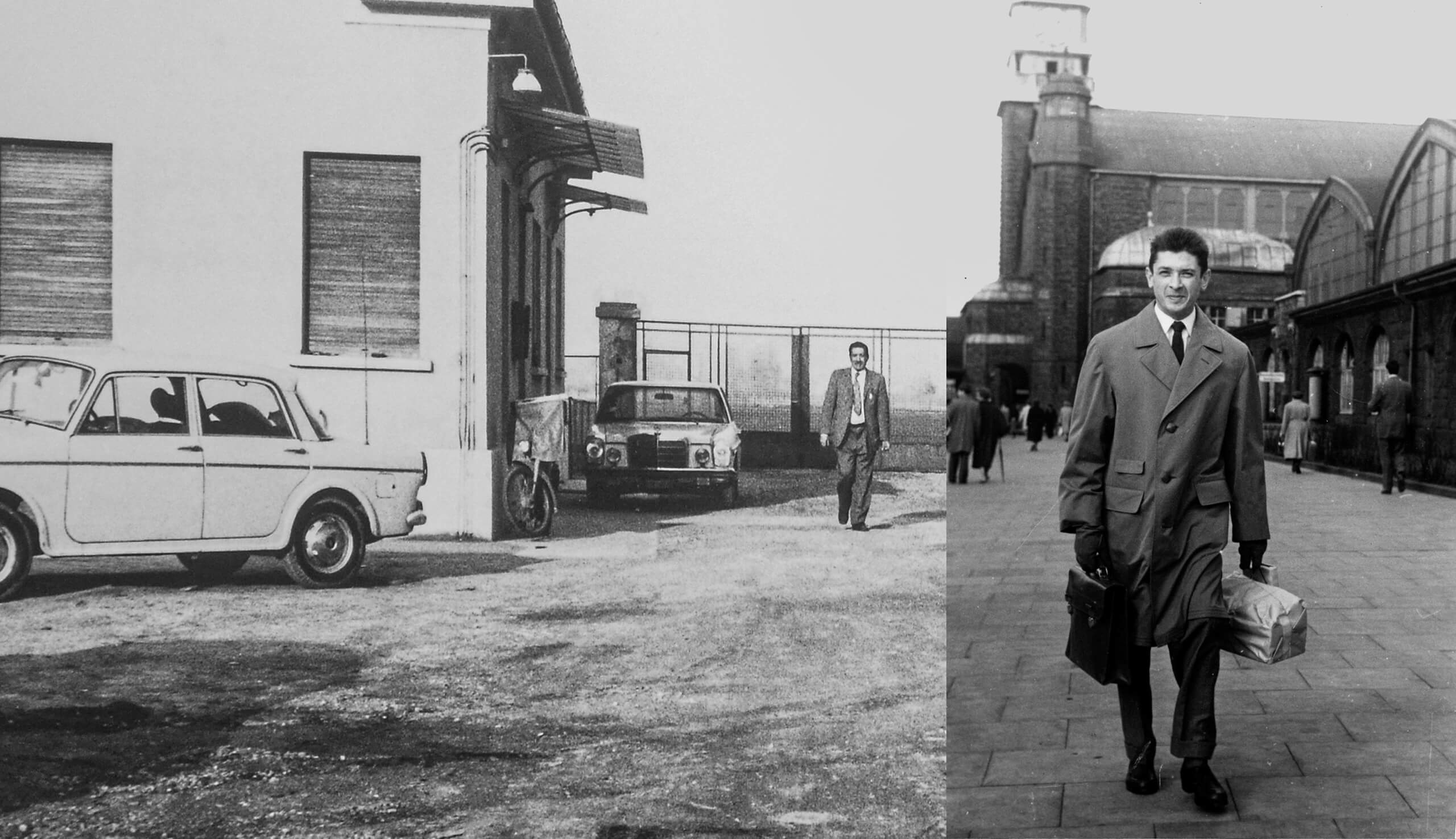
What remains after the rice harvest
Rice has been grown in Piedmont since the 15th century. Today, the world’s most important grain is a significant agricultural factor in the region. Numerous rice-husking mills are in operation, on whose premises huge amounts of rice husks build up: The husks are the processing „waste“.
In the past, the rice husks (spelt) were simply burned on the rice fields after harvesting and processing. However, because rice husks have a very high calorific value, the idea came up to use them to produce energy, some of which was used to generate steam for the production of parboiled rice directly in the husking mills, and later in biomass power plants.
And doesn’t melt so easily
The residues after incineration have a skeletal structure consisting of biogenic silica. Biogenic silica is chemically very pure, with a content of 92…97 % silicon oxide. Consequently, it has a very high melting point. Precisely what Alexander Tutsek was searching for.
Many years later, Danilo Bertolotti will use this potential for innovative refractory technology that makes use of a particularly up-to-date advantage.
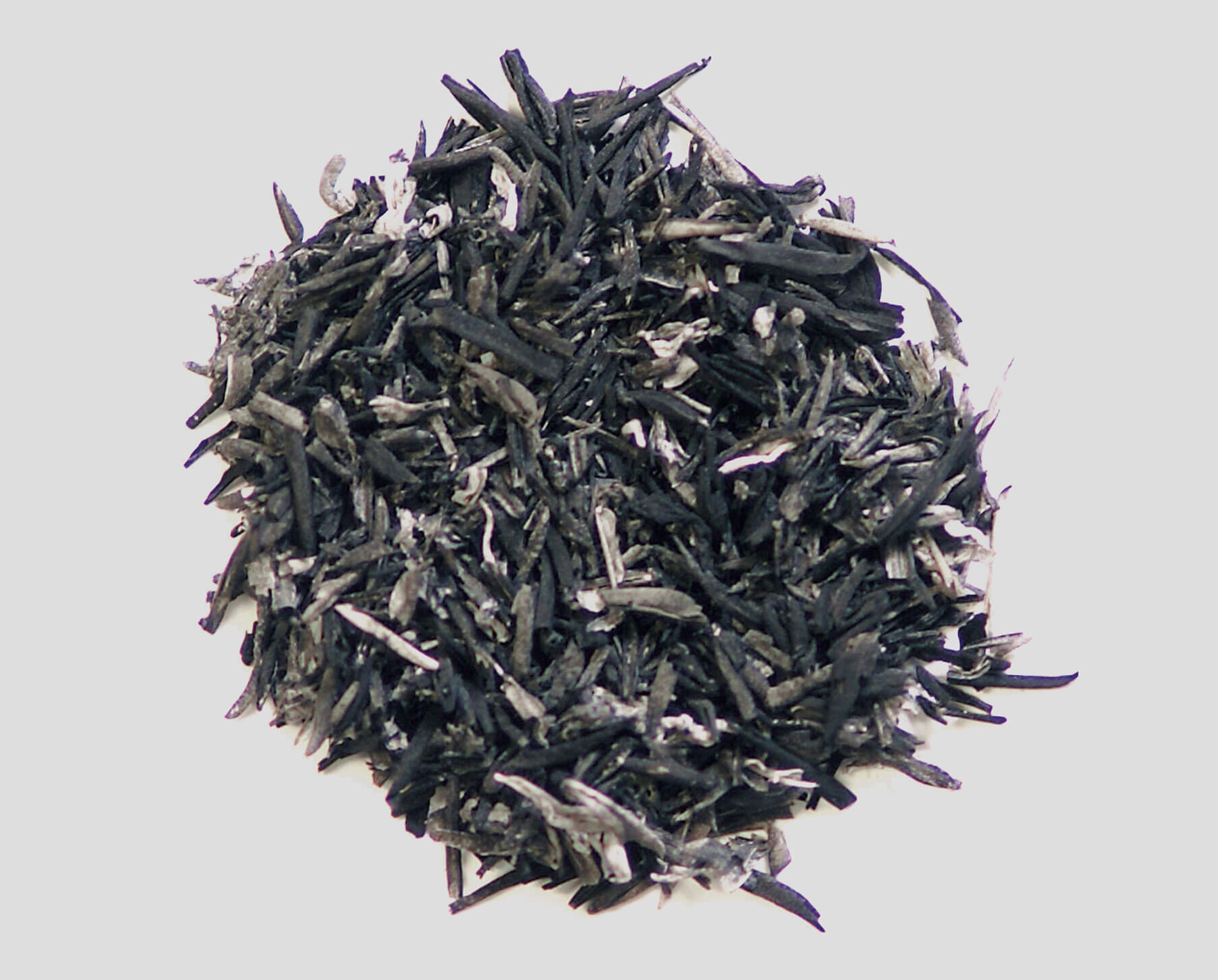
An encounter with consequences
When Alexander Tutsek took a trip to Italy on a later occasion, and Danilo’s father was unable to meet him at the airport, the latter asked his son to help out. The result of these two men meeting was that the use of rice husks found its way into completely new fields. Soon after, young Danilo moved to Refratechnik in Göttingen (Lower Saxony), Germany. Several years of learning followed, plus intensive work on biogenic silica as a refractory raw material.
Together with his colleagues in the research and development departments, Danilo Bertolotti carries out test series and examines the material’s open porosity. As a result, the outstanding insulating properties of rice husk ash at high temperatures can be confirmed. Rice husk ash exhibits extraordinary refractory properties.
The road to a marketable product is paved.
Amazement in the steelworks
During the development phase, at the end of which a refractory product made of rice husk ash is hoped for, Danilo Bertolotti visits a steelworks. For test purposes, he requests that a 10 cm thick layer of biogenic silica is spread over liquid molten metal.
The steelworkers nearby watch the proceedings with skeptical looks. Some of them wonder: „What is a bit of rice husk ash expected to bring about?“
Measurements provide precise answers: The temperature of the molten steel under the insulating layer is 1600 °C, while on top of the layer it is hardly 50 °C.
What Danilo Bertolotti had already expected, is a sensation for the bystanders.
Market-oriented innovation
Following the test phase, Danilo Bertolotti takes over control of the project: During the next years, rice husk ash is developed into a truly innovative refractory solution. The 1st generation of biogenic silica products to be launched on the world markets are the qualified process materials NERMAT® and the low-carbon SILIMAT®.
Qualification of biogenic silica is based on the technology – and leads to its success. Since 40 years, NERMAT® AF is the classical covering material for the thermal insulation of tundishes and casting ladles, and has set worldwide standards for quality and efficiency.
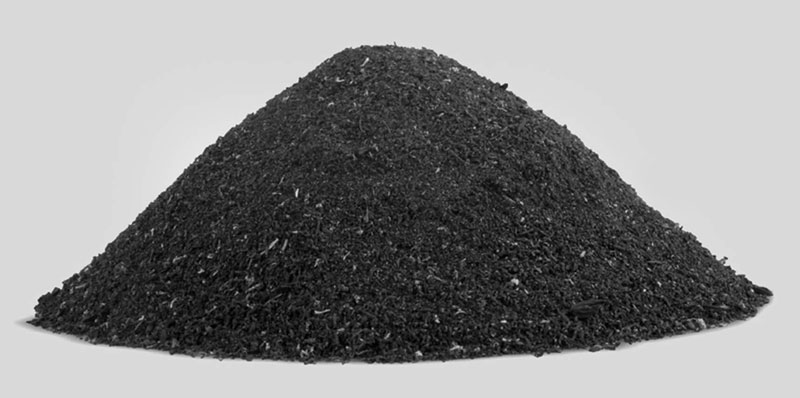
Ash to granulate
Meanwhile, Danilo Bertolotti invested his technical expertise and creativity into further development work. He intends to overcome the tendency of rice husk ash to generate dust. This leads to a new idea: Biogenic silica in the form of granulates that are correspondingly free of dust. As a result, the special product NERMAT® G is developed.
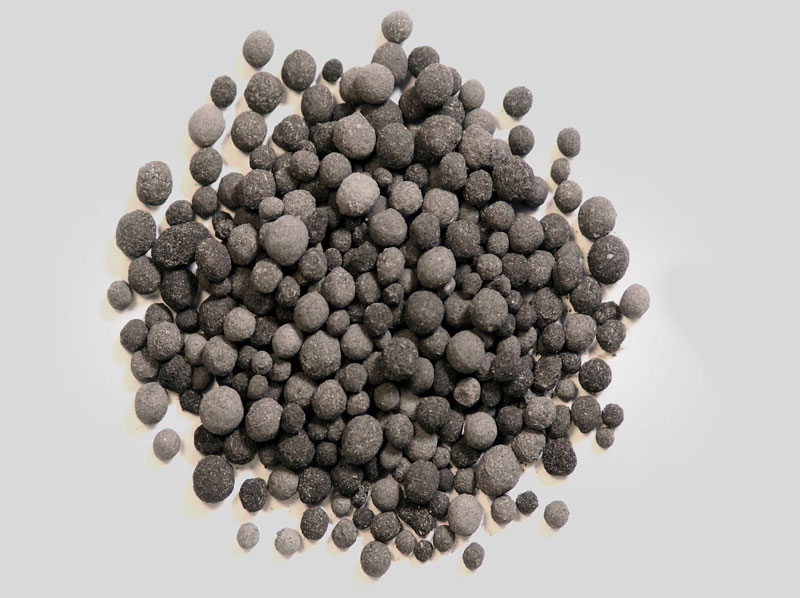
Ash to panels
The latest step in development is done by the team in Düsseldorf, Germany: Rice husk ash as a product that can be cut and drilled. PROLITE® is a shaped and pressed panel made of biogenic silica. The highly insulating panels are suitable for use in a wide range of industrial applications. They are a dust-free alternative for insulating material in direct contact with hot media.
Refratechnik offers them as decomposing panels for one-time insulation, or as permanent panels for continuous use.
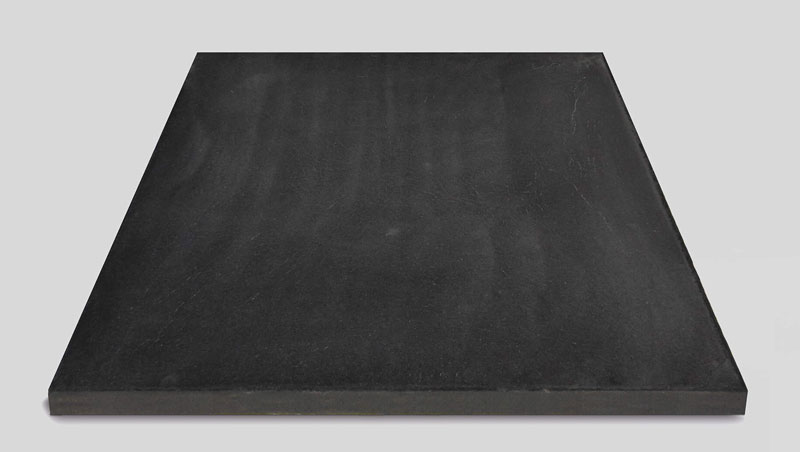
PROLITE® for outstanding insulation. Sustainably produced.
Danilo Bertolotti soon recognized that apart from its outstanding insulating properties and low weight, the formability of rice husk ash into different shapes represents a decisive product advantage. Consequently, Refratechnik focuses on sustainability and the intelligent use of resources – an increasingly important aspect for today’s industry in future.
Therefore, this newest and most innovative product based on rice husk ash complies precisely with this farsighted perspective: PROLITE® can also be used in the form of lightweight refractory bricks that are ideally suited e.g. for backup insulation. PROLITE® permits temperature reductions of up to 80 %, and can be used with temperatures up to 1600 °C. Its alkali resistance is very good. Moreover, its dust-free processability contributes to better occupational safety.
Based on a naturally renewable raw material.
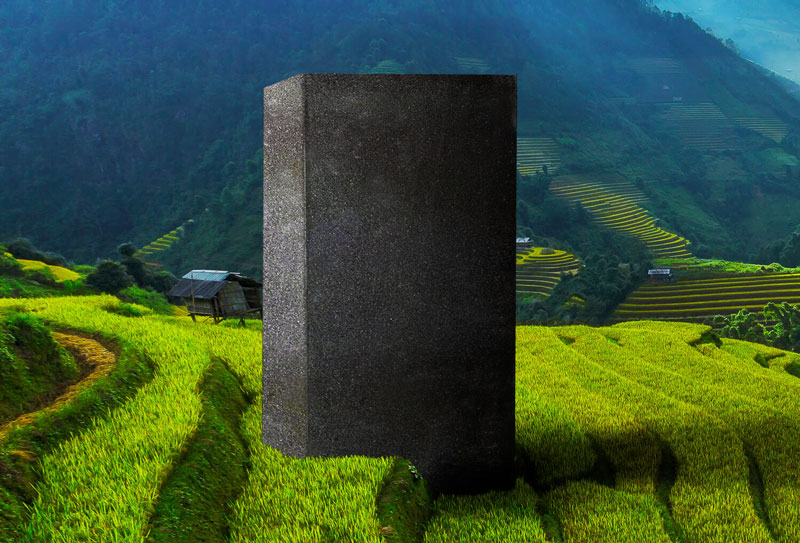
Consistently sustainable
In terms of sustainability, PROLITE® follows a consistent approach: Rice husks are used in modern biomass power plants as a quality-controlled source of energy.
Hereby, the raw material is burned in a carbon-neutral manner. This means that during combustion, no more CO2 is released than the rice plant absorbed from the atmosphere during its growth. During production, the volatile constituents are incinerated, but without destroying the microporous structure of the SiO2 that ensures the outstanding insulation properties. It has a low carbon content, is amorphous, and not respirable.
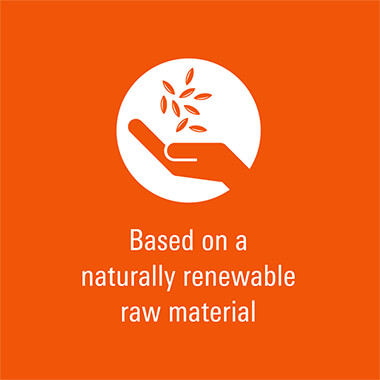
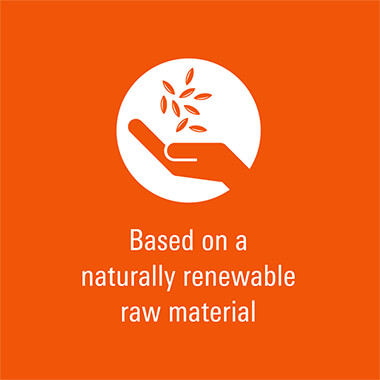
Innovatively into the future
The promotion of new refractory technologies that permit sustainable raw material use, is a central issue of Refratechnik’s research and development work. Danilo Bertolotti’s pioneering work has inspired our company to implement rice husk ash in an increasing number of applications.
In this way, Refratechnik is a partner for companies involved in the systematic improvement of their life cycle assessment.
The activities of Alexander Tutsek, and the ideas of Danilo Bertolotti are synonymous for the innovative drive we experience every day, and will be continued by the next „Refratechnik generation“.
Expect the best. Refratechnik